Behind every successful shipment here at SmartShield - and indeed in the wider packaging world - lies a tale of exceptional packaging.
At SmartShield, we excel not only in providing reliable packaging solutions that ensure safe delivery but also in custom-cut packaging.
Our expertise in this area involves crafting protective solutions from foam, cardboard, plywood, corrugated plastic, and plastic HDPE items. Quality custom-cut packaging is often vital for adding an extra level of safeguarding to high-value packages during transit.
Take for example, these foam inserts we created for a client for use in a heavy-duty Pelican case, and a honeycomb corner fabricated for door protection, below.
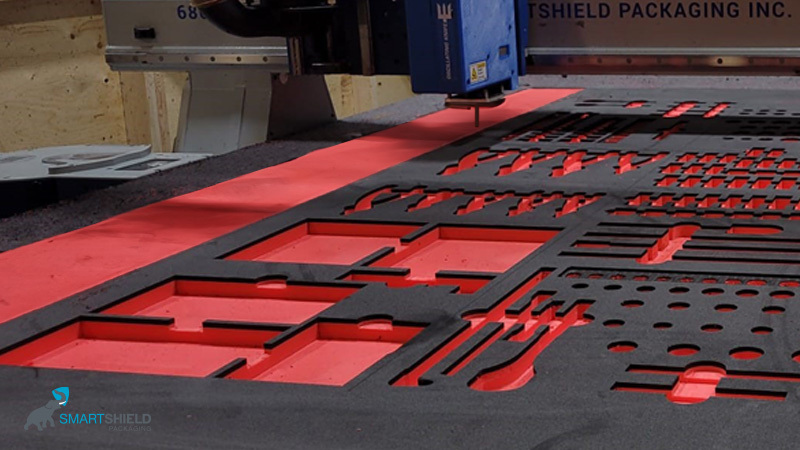
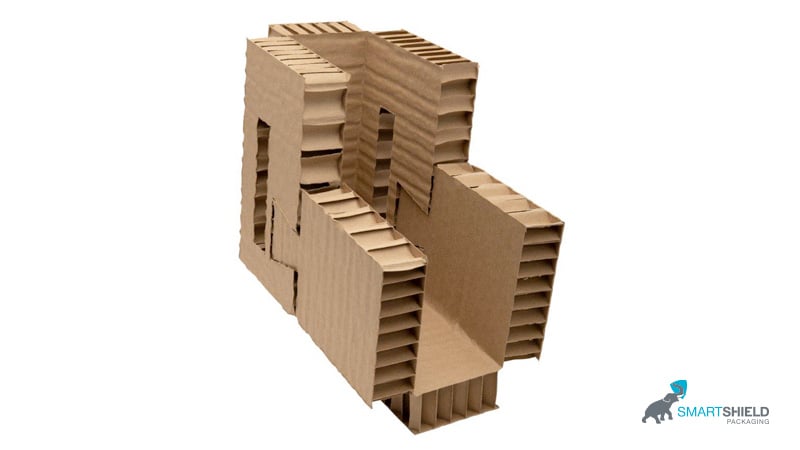
Whether it's delicate electronics, aerospace components, or automotive parts, we’re helping to protect, we anticipate that our packages will face bumps, jolts, and unexpected twists along their journey.
Yet, we've earned a reputation for ensuring critical packages reach their destination unscathed. And a significant part of this success is owed to those meticulously crafted custom-cut designs.
Two common methods are employed for creating custom-cut packaging: router cutting / CNC knife cutting, and waterjet cutting. But why should you care whether the protective inserts in your package are waterjet or knife/router cut?
Let's dive into the subject and uncover the distinctions between each technique.
What is waterjet cutting?
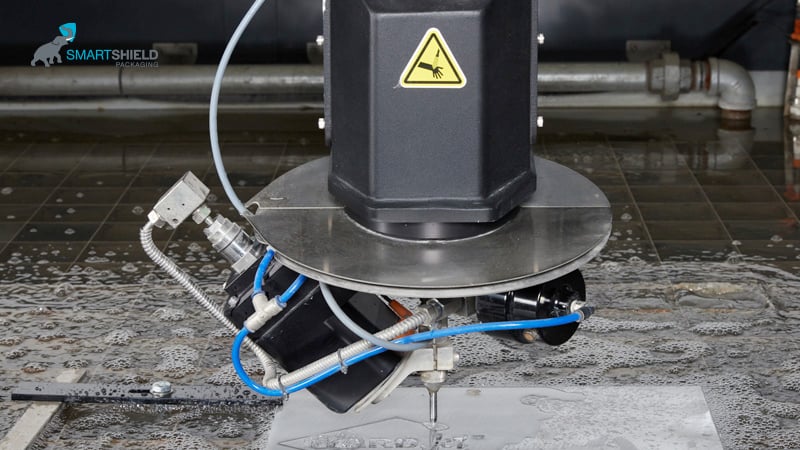
This method entails a high-pressure jet of water to slice through materials. Known for its precision and versatility, waterjet cutting can handle a broad array of materials, in addition to foam, including plastics, stencil board, and metals.
It delivers clean, precise cuts without generating heat, making it ideal for sensitive materials or intricate designs - like the foam pieces with angled cuts, below.
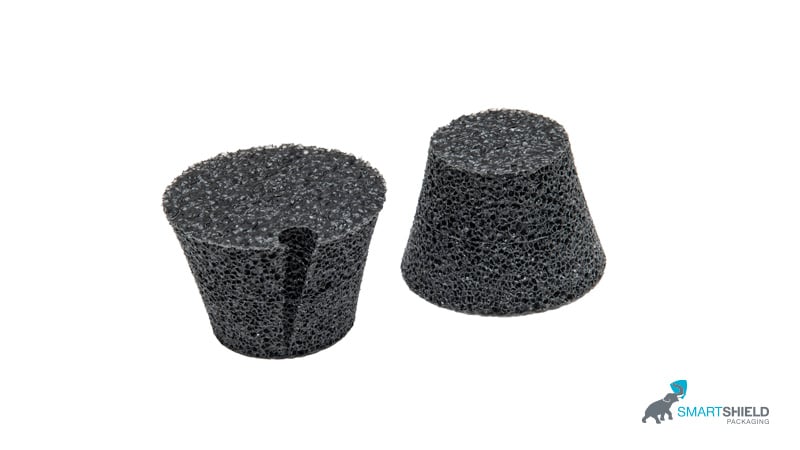
What is CNC knife/router cutting?
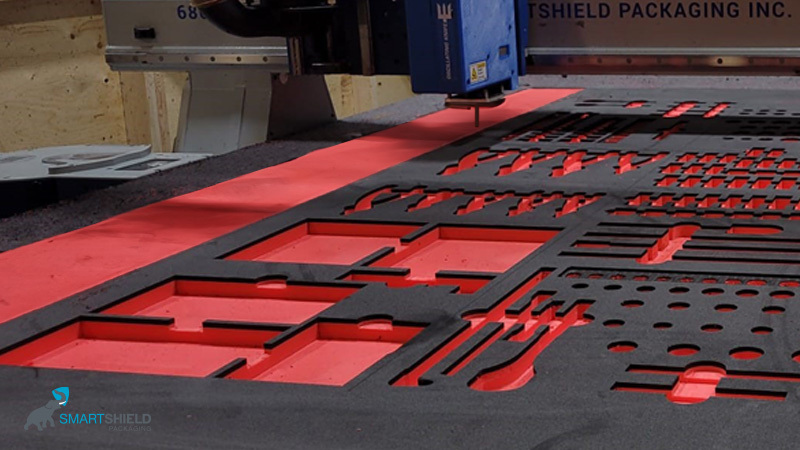
In this method, a sharp knife or router tool is employed to slice through packaging materials. Knife cutting is effective for swiftly producing straight cuts or complex shapes in materials including foam, cardboard, corrugated plastic and rubber. The knife can also be replaced with a scoring wheel to enable us to score cardboard and corrugated plastic materials.
Router cutting, conversely, employs a rotating cutting tool to carve out shapes or patterns in foam, wood and plastic.
Take a look at some examples in the images below.
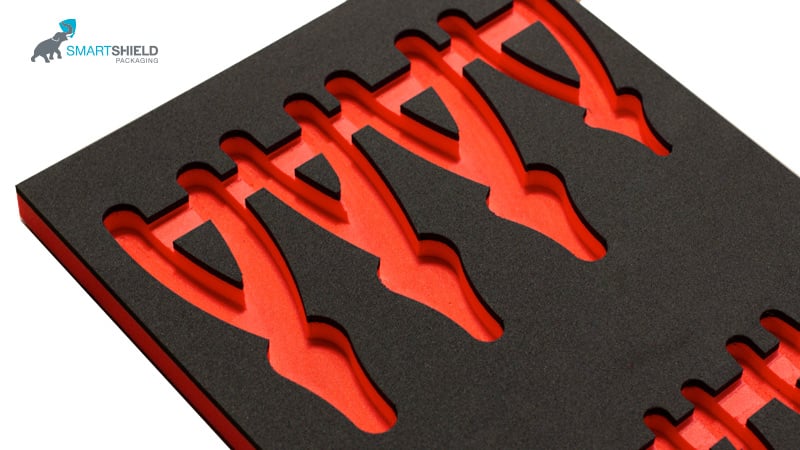
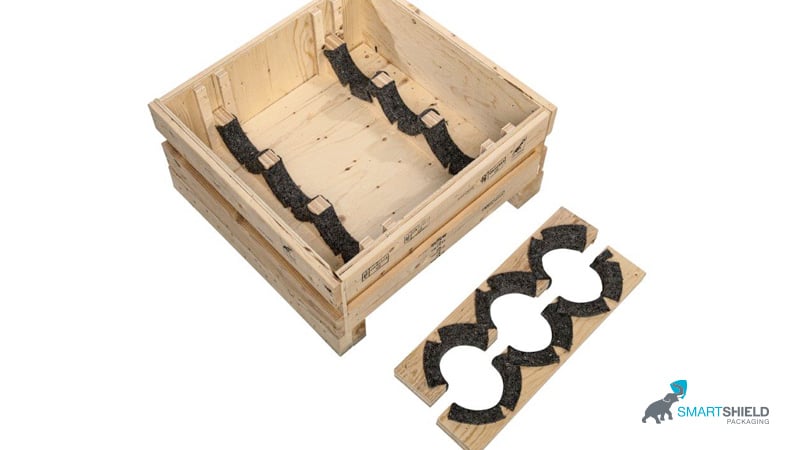
Now, let’s delve into the pros and cons of each:
CNC knife/router cutting advantages
- Precision: this method achieves perfectly accurate pocket dimensions and precise material thicknesses, as it also has the capacity to make partial cuts into the material without cutting all the way through when required. (Unlike waterjet)
- Efficiency: We can maximize the machine’s efficiency by having a range of tools to choose from, so we can create products faster.
- Versatility: this method is capable of 3D routing and crafting complex contours.
- Customization: automated tool changers enable additional features like bevels or chamfers.
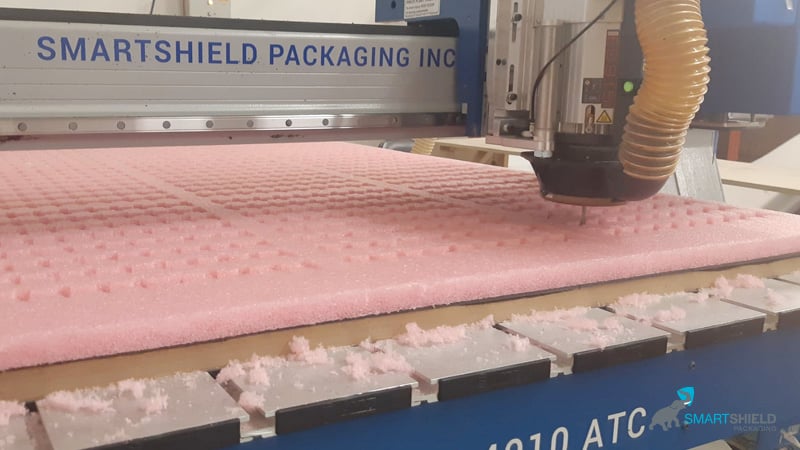
Disadvantages:
- The machine doesn’t cut through material as rapidly as other machinery can
When cutting certain materials excess heat can cause cutting challenges resulting in poor cutting quality, or an unclean finish.
- Material has to be vacuumed or fixed to the cutting surface to be able to successfully machine.
Waterjet cutting advantages
- Edge Precision: this method delivers smooth, burr-free edges, ideal for intricate designs.
- Cutting Precision: As this machine has 5-axis capabilities, it can be used to cut beveled contours, which ensures a more precise fitment than other machines.
- Efficiency: there are no tool changes required, which reduces downtime and enhances efficiency. Plus, the machine is capable of cutting multiple sheets at the same time, increasing production output.
- Material Utilization: waterjet cutting is efficient in terms of maximizing the usage of the material being cut. This is because, unlike other cutting machines, it can cut all the way to the edge of the sheets, translating into cost savings and environmental benefits.
Disadvantages:
- The depth of cutting can’t be controlled, meaning this machine can only be used to cut entirely through the material.
- When cutting dense materials the machine has to be slowed down, to ensure a clean cut edge.
- It’s more expensive than CNC Knife/Router cutting
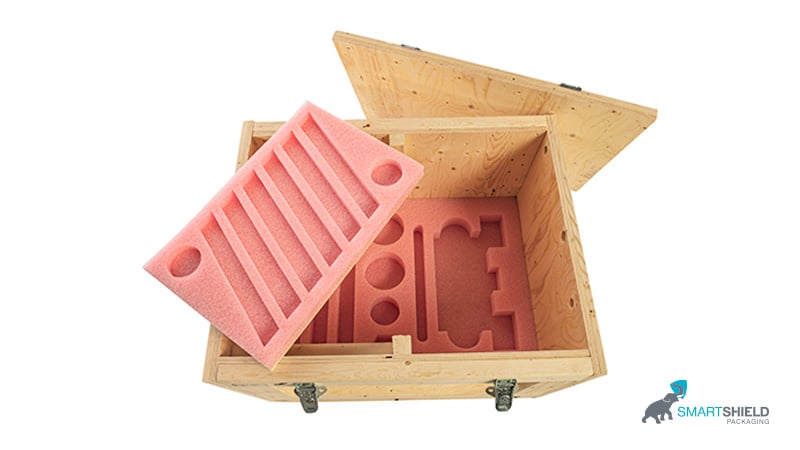
Cost considerations of CNC knife/router cutting
When it comes to selecting the right cutting method for your customized packaging solution, cost is a crucial factor to consider.
In general, the CNC knife/router cutting method tends to have lower initial equipment costs compared to waterjet cutting machines.
Additionally, CNC knife/router cutting may offer lower operating expenses, as it typically requires less energy consumption and maintenance compared to waterjet cutting.
However, it's essential to weigh these upfront savings against potential long-term costs.
Cost considerations of waterjet cutting
While waterjet cutting may have higher initial investment and operating costs, its efficiency in material utilization can lead to reduced material waste, ultimately offering cost savings over time.
Furthermore, waterjet cutting's versatility and ability to handle a wide range of materials may contribute to overall cost-effectiveness by eliminating the need for multiple cutting methods.
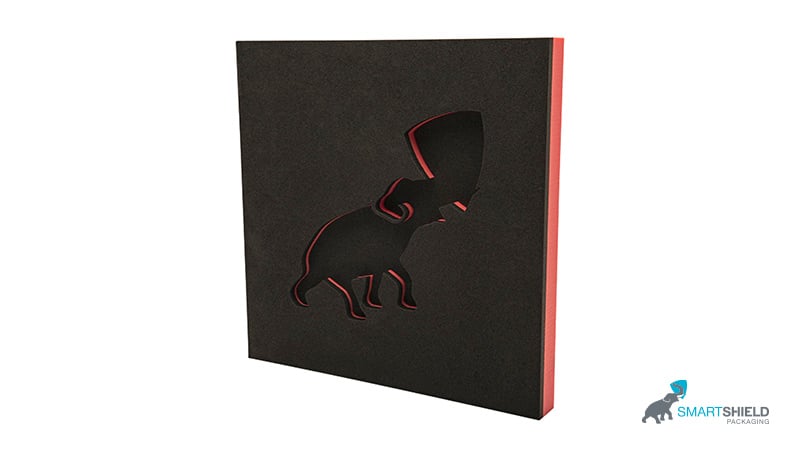
Knife cutting or waterjet cutting for your custom-cut packaging? To sum up...
At SmartShield, we understand that every curve, every contour of your shipment matters, which is why choosing between router/ knife cutting vs. waterjet cutting for your custom-cut packaging is an important consideration.
The difference between these methods can significantly impact the precision, efficiency, and cost of your packaging solution. And choosing the right method is important because it ensures your packaging meets your specific needs, and reassures you that your goods are in good hands from start to finish.
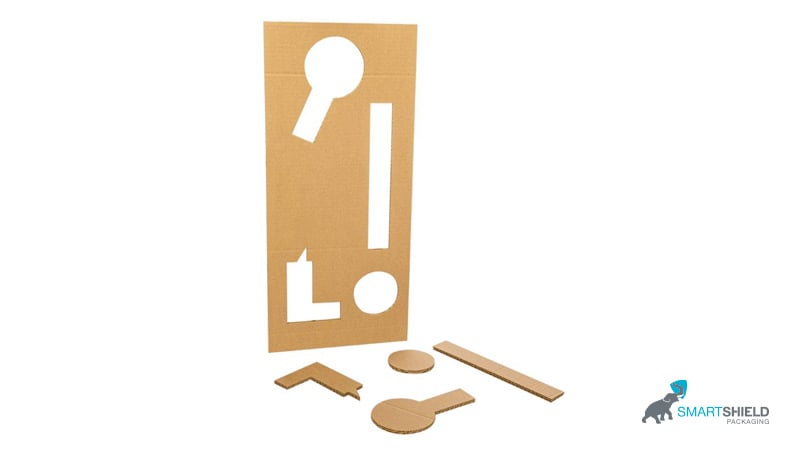
As we’ve seen, both CNC knife/router cutting and waterjet cutting offer unique advantages for custom packaging. While CNC knife/router cutting excels in precision and versatility, waterjet cutting boasts faster cutting speeds and efficiency, as well as beveled cutting capabilities.
The choice between these techniques obviously depends on your specific project requirements, material properties, and budget considerations - and is not a one-size fits all choice.
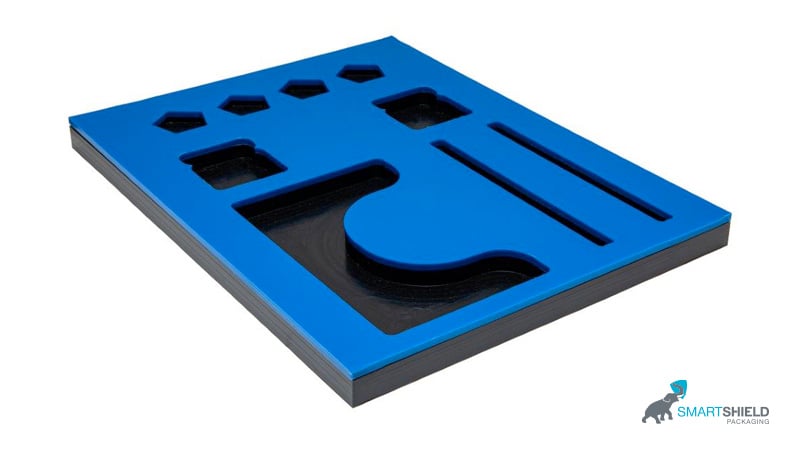
However, we hope this blog has shed some light on the differences between the two to help you make more informed decisions.
Remember, we're here to help you make the right choice, too - and you can get in touch with our friendly team at any time.