When Avidrone Aerospace reached out, they weren’t just looking for packaging: they needed a solution as innovative as their drones.
Avidrone’s aren’t off-the-shelf UAVs but high-performance, heavy-lift machines built for serious missions, and protecting them during transport called for more than standard materials.
From delicate electronics to carbon fiber rotors, every part had to be secured using a custom protective packaging system designed for both conventional shipping and rugged field deployment. That’s where Team SmartShield came in!
This project wasn’t about putting foam in a box. It was about engineering a precision-fit system that cradled sensitive equipment, prevented transit damage, and looked professional every time it was unpacked.
Let’s take a look at how we delivered…
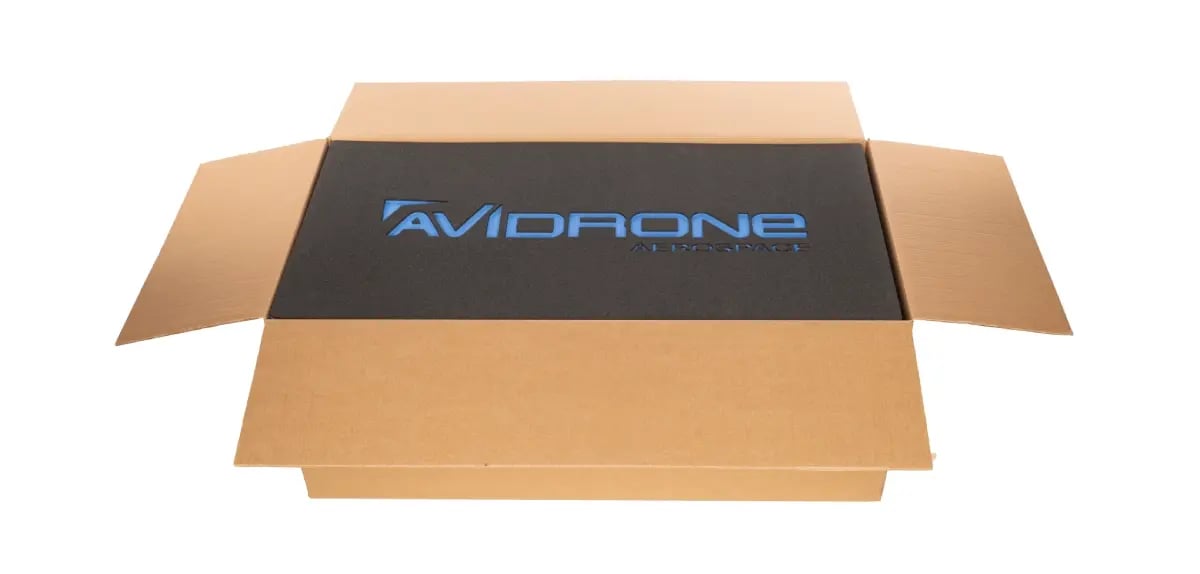
Understanding Avidrone’s Custom Packaging Challenges
Avidrone builds impressive drones: long-range, tandem-rotor machines that can carry a significant load across really remote terrain. But with that kind of performance comes a lot of complexity, especially when it comes to shipping.
Each drone is made up of all kinds of sensitive parts: carbon fiber frames, rotors, sensors, electronics, and more. And every one of those components has its own shape, size, and fragility.
Secure packaging during transit is non-negotiable.
The kicker? Avidrone needed one packaging setup that worked in two totally different ways. They wanted foam inserts that could fit both into regular shipping boxes and into rugged hard cases for field use, the kind that can take a serious beating.
Our job was to design a lightweight, reusable packaging solution that was modular, easy to handle, and rugged enough for field conditions. It had to protect everything properly, but still be easy for the Avidrone team to use, whether they were shipping across the country or carrying gear into the field.
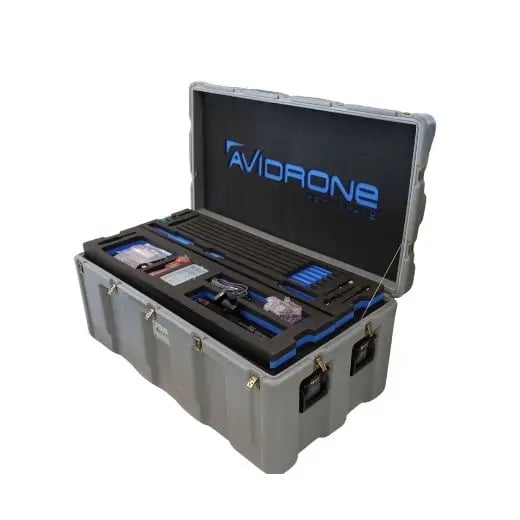
Our Tailored Packaging Solution
To meet all of these requirements, we engineered a custom foam packaging system using premium materials and precision processes:
As always, we started with collaboration. Our engineers worked closely with Avidrone’s team to study the drone’s geometry, support points, and vulnerable areas. From there, we prototyped and iterated until we landed on a solution that checked every box.
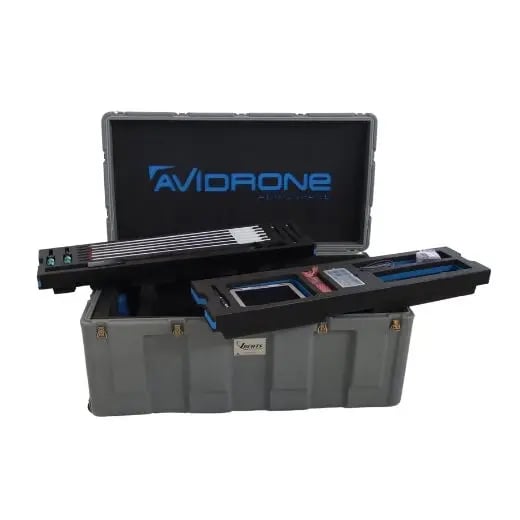
Here’s everything we delivered:
Six-Piece Custom Foam Insert Set
We created a precision-cut insert system from dual-colour Zotefoam, a popular shock-absorbing foam insert material often used in aerospace packaging. Each piece interlocks to fully surround and suspend the drone parts, keeping them safe from impact on all sides.
3D-Routed Trays
Using CNC routing, we cut exact pockets for each drone component. These contours were designed to support the UAV at strong structural points, while allowing delicate elements like blades and sensors to remain untouched, suspended safely in place. This CNC-cut foam design ensured each part was supported where it needed it most.
Reinforced Foam Inserts
For heavier drone parts, we added integrated plastic panels laminated into the foam. These built-in supports act like an internal skeleton, keeping the insert rigid under pressure and maintaining its form through repeated use.
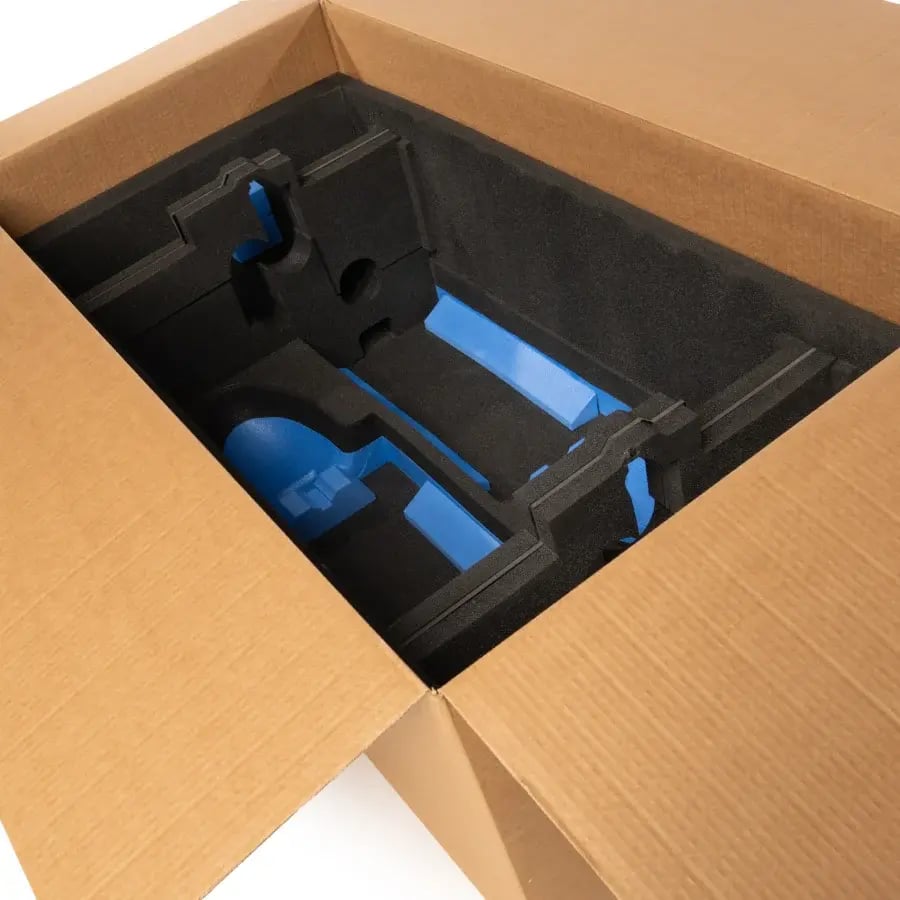
Dual-Case Compatibility
Each insert was designed to drop neatly into either a standard shipping box or hard shell case, giving Avidrone the flexibility to use the same set for both delivery and field operations.
User-Friendly Fit
Every piece is numbered and fits only one way, making packing and unpacking simple. And the dual-colour design gives quick visual confirmation that nothing has been missed.
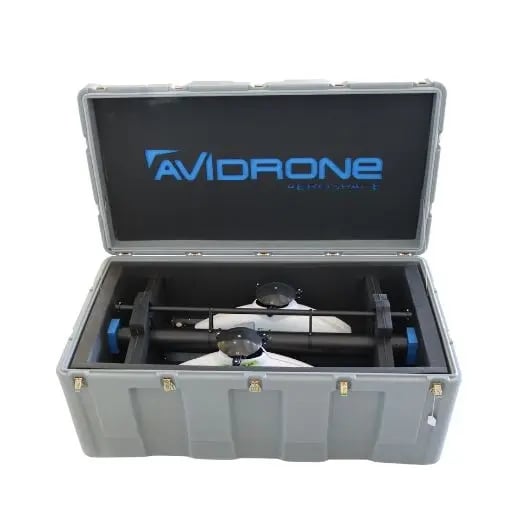
The Results
Once everything came together, the final engineered packaging solution did exactly what it needed to. It didn’t just protect the drones during shipping; it added real value to how Avidrone presents and handles their products.
Here’s what stood out once the new system was in use:
- Durability: The foam inserts held up to all kinds of handling - vibration, drops, you name it - without losing their shape. Even the heavier drone components were supported properly, thanks to the reinforced panels we built into key areas.
- Protection: Every part of the drone, from delicate sensors to large structural pieces, stayed locked in place. No shifting, no rattling: just solid, consistent protection during transit.
- Portability: The dual-use design worked exactly as planned. Avidrone could use the same insert set for both standard shipping boxes and rugged hard cases, making it easy to switch between delivery and field deployment without repacking.
- Presentation: This wasn’t just about function—it looked great, too. The dual-colour foam gave everything a clean, professional finish. When a client or operator opened the case, it was immediately clear that the product inside was treated with care.
As Avidrone told us, the new packaging gave them “confidence that the product would arrive as perfect as it left.” And that’s exactly what we aim for.
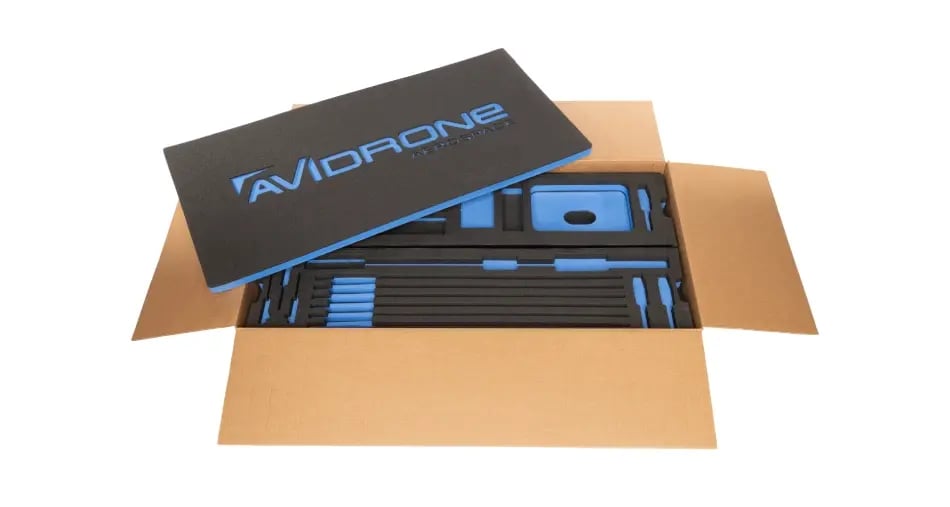
Looking Ahead
This project is a great example of what we like doing most: collaborating with innovators in aerospace and defense to build packaging that performs as well as the product inside.
Whether it’s a high-tech drone, medical equipment, or sensitive electronics, our team is always ready to create solutions that are custom-engineered, field-tested, and built to impress.

Got a product that needs to go places, safely and securely? SmartShield’s ready to design a custom solution that protects what matters most.